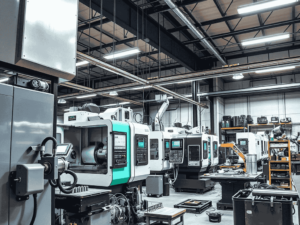
Precision Metal Fabrication Capabilities
MW+ delivers end-to-end CNC machining, fabrication, and finishing services with ISO-certified quality, fast turnaround, and unmatched precision.
Request a Quote?
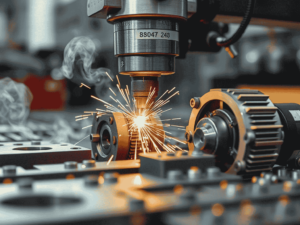
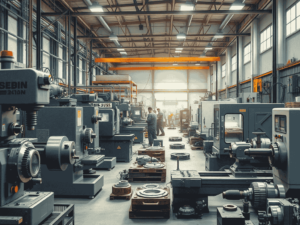
Minimum Order Quantity (MOQ)
We offer a flexible minimum order to accommodate small or prototype requests.
Total Parts Produced
This metric indicates total parts produced, demonstrating our efficiency.
Design
Variety
Choose from over 6,000 unique designs for every preference.
Shipping Availability
We provide worldwide shipping for global accessibility.
Manufacturing Capabilities
Precision Engineering for Complex Part Requirements
Equipment & Technology
We invest in cutting-edge machinery and advanced manufacturing technologies to deliver precision, efficiency, and scalability. State-of-the-art equipment enables us to handle complex geometries, tight tolerances with consistent quality.
Our Manufacturing Technology
- Multi-Axis CNC Machining Systems – High-speed, high-accuracy milling and turning centers capable of complex geometries and tight tolerances
Precision Swiss-Style Lathes – Specialized equipment for micro-machining and high-volume small part production
Electrical Discharge Machining (EDM) – Advanced wire and sinker EDM systems for intricate cuts in hardened materials
Automated Metrology & Inspection – State-of-the-art coordinate measuring machines (CMM) and optical comparators for quality validation
Additive Manufacturing Solutions – Direct metal laser sintering (DMLS) and selective laser melting (SLM) for rapid prototyping and production.
Capacity & scalabilities
We combine robust production capacity with flexible scalability to meet your evolving manufacturing needs—from rapid prototyping to full-scale production runs.
Our Production Capabilities
- High-Volume Capacity
- 50+ CNC machines operating 24/5
- Dedicated production cells for batch runs up to 50,000+ units
- Automated finishing lines for consistent throughput
- Precision Scalability
- Seamless transition from prototype (1-10 units) to production (10,000+)
- Agile manufacturing systems for mid-volume runs (100-5,000 units)
- Just-in-Time (JIT) and Kanban inventory management
- Operational Flexibility
- 30% surge capacity for urgent projects
- Dual-shift capabilities for accelerated deliveries
- Distributed manufacturing network for geographic redundancy
Material Expertise
Our machines handle a wide range of materials with precision and efficiency, ensuring top-quality results for every industry.
Our Material Capabilities
- Metals & Alloys
- Aluminum (6061-T6, 7075) & Stainless (304/316L, 17-4PH)
- Titanium, Inconel, Tool Steels (D2, A2)
- Engineering Plastics & Specialties
- PEEK, Ultem, PTFE, Tungsten
- Carbide, Magnesium, Copper Alloys
- Value-Added Services
- Full material certifications & heat treating
- Corrosion testing & DFM support
Project Workflow
Our project workflow ensures a seamless manufacturing process from concept to completion. We start with a needs assessment and design phase, collaborating closely with clients to refine specifications
Project Workflow
- Needs Assessment: Collaborate with clients to define project specifications and requirements.
- Design & Prototyping: Utilize advanced software to create precise models for client approval.
- Production: Employ state-of-the-art technologies and skilled personnel to manufacture components.
- Quality Control: Implement rigorous testing and inspection throughout the production process.
- Communication: Provide regular updates, ensuring transparency and addressing any concerns promptly.
- Logistics & Delivery: Guarantee timely delivery with options for assembly and installation as needed.
Engineering-Grade Materials
We work with a diverse selection of materials for our services, including various metals and specialized alloys. Choose from options such as steel, aluminum, brass, and more to create custom products that meet your specific production needs.
Customization and Engineering Support
Precision Machine Tool Maintenance and Retrofitting
Maintain optimal machine performance with structured maintenance programs and expert retrofitting, reducing downtime by up to 30% and extending machine life by 5–10 years.
Key Capabilities:
Over 95% uptime achieved with scheduled maintenance plans
Full mechanical/electrical retrofits for machines aged 5–20+ years
Accuracy restored to within ±0.005 mm via alignment and calibration
Cost savings of up to 60% compared to new equipment investment
Customized retrofit solutions for CNC and conventional systems
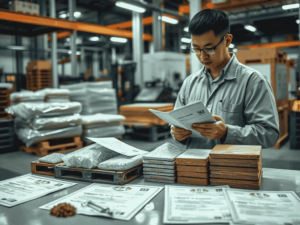
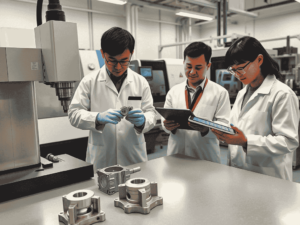
Automation & Smart Machine Integration
Boost machining productivity by up to 50% with integrated automation systems engineered to streamline complex and repetitive tasks with high precision.
Key Capabilities:
Robotics and PLC integration improve output consistency by 40%
CNC automation reduces cycle times by 20–35%
Data-driven control systems ensure real-time performance feedback
Lights-out manufacturing enabled for 24/7 operation
ROI within 12–18 months through labor and time efficiency
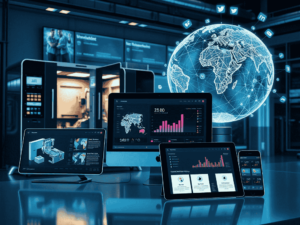
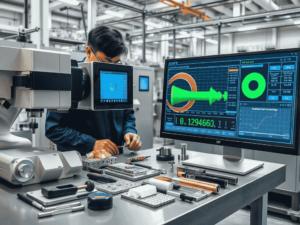
Custom Machining Solutions for Specialized Applications
Our tailored machining solutions have improved part quality and consistency for over 200+ customized projects, enabling clients to meet the tightest tolerances and unique specifications.
Key Capabilities:
Custom fixtures reduce setup time by up to 45%
Jigs and tool modifications enhance repeatability by ±0.003 mm
Designed over 150+ custom tooling systems across industries
Support for batch sizes from 1-off prototypes to 10,000+ units
Compatibility with materials including titanium, stainless steel, and composites
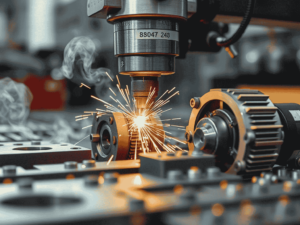
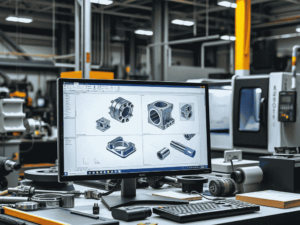
Engineering Support for Precision Manufacturing Optimization
Our engineering expertise has helped clients reduce cycle times by up to 35% and improve production throughput by 25–40% through data-driven optimization and process refinement.
Key Capabilities:
Process audits completed for over 100+ machining facilities
CAM optimization reduces programming time by 20–30%
Quality improvement initiatives achieving defect rates <0.5%
Customized toolpath strategies cut material waste by up to 20%
Real-time diagnostics and troubleshooting for performance stability
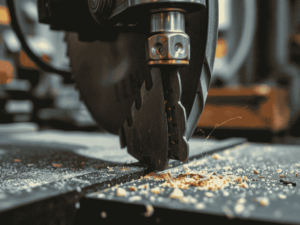
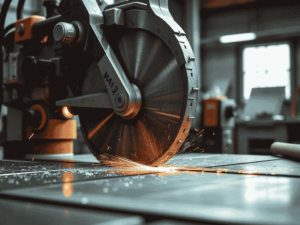
Custom Precision Machine Tool Design and Development
We have successfully delivered more than 80+ custom-built precision machines tailored to demanding applications, offering superior performance and repeatability within ±0.001 mm tolerance.
Key Capabilities:
End-to-end design-to-build cycle within 90–150 days
Multi-axis capabilities, up to 5-axis machining integration
Engineered systems with speeds up to 24,000 RPM
Modular designs for flexible upgrades and retrofits
Fully tested and validated for ISO and industry compliance
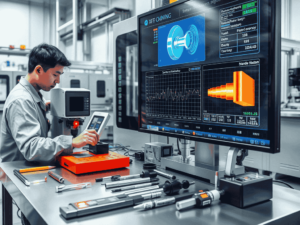
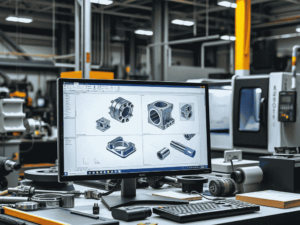
Products Expertise
Precision Elements
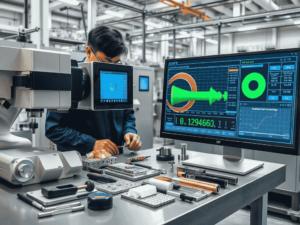
We specialize in high-precision components designed for accuracy, durability, and efficiency. Our expertise ensures tight tolerances and superior performance for critical applications..
Materials Selection
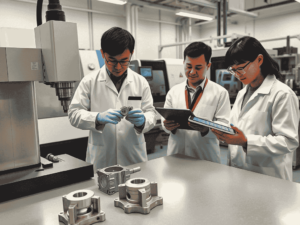
Choosing the right materials is crucial for product reliability and longevity. We provide expert guidance in selecting optimal materials based on mechanical properties, environmental conditions, and industry standards. and respect customer decision.
Testing Validation
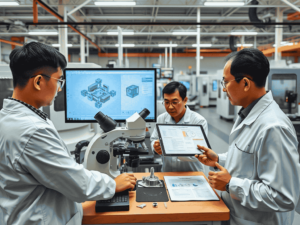
Our rigorous testing and validation processes ensure product quality, performance, and compliance. We conduct detailed inspections, simulations, and real-world testing to guarantee reliability and safety..
Process Optimization
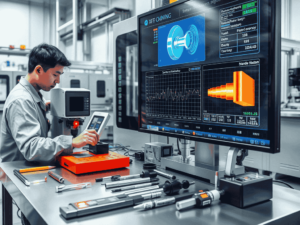
We help enhance manufacturing efficiency through process optimization. By refining workflows, reducing waste, and improving productivity, we ensure cost-effective and high-quality production.




Our Manufacturing process
Our manufacturing process combines precision engineering, advanced machinery, and strict quality control to deliver reliable, high-performance metal components.




